SAP PLM
1.Introduction
1.1 Background and Evolution of SAP PLM
SAP PLM (Product Lifecycle Management) is an integral component of the SAP ecosystem, designed to manage the entire lifecycle of a product from its inception to its market withdrawal. With roots tracing back to the early days of enterprise software, SAP PLM has undergone significant evolution. Initially focused on product data management, the system has expanded its scope to include project management, quality, and environmental compliance. This evolution has been carried out to adapt to changing market needs and the increasing demands of digitalization and sustainability.
1.2 Relevance of SAP PLM in the SAP Solutions Ecosystem
Within the SAP solutions ecosystem, PLM plays a crucial role by efficiently integrating with other modules such as SAP ERP, SAP SCM (Supply Chain Management), and SAP CRM (Customer Relationship Management). This integration allows companies to obtain a coherent and centralized view of their operations and products. It not only facilitates product development and quality management but also improves strategic decision-making based on accurate and real-time data.
SAP PLM has become an essential tool for companies looking to drive innovation and comply with complex and changing regulations. Its ability to handle various aspects of the product lifecycle makes it invaluable for any growth and efficiency-oriented company.
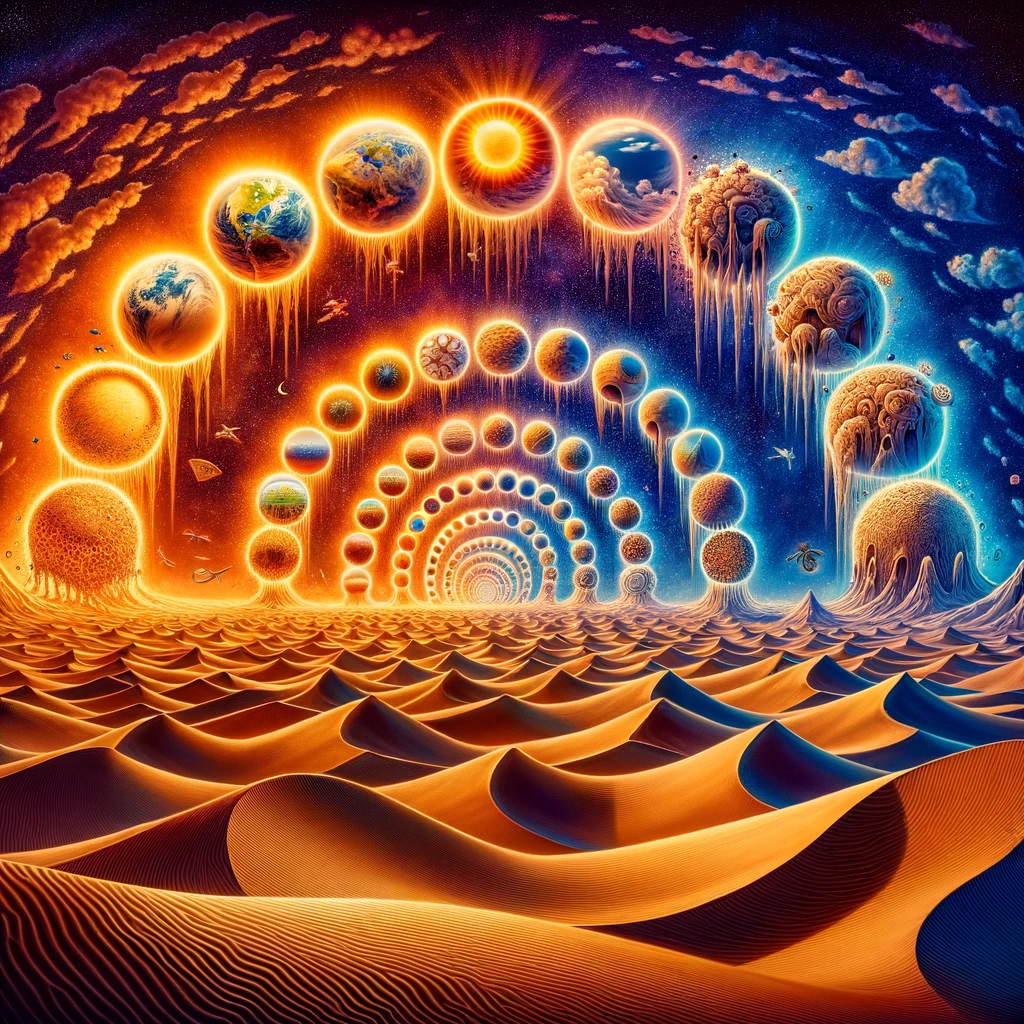
2.Key Components of SAP PLM
2.1 Product Lifecycle Management
Product lifecycle management is a central element of SAP PLM and acts as a pillar for nearly all operations linked to the development and maintenance of products.
Key features:
- Design and Development: SAP PLM facilitates the product design and development process, allowing multidisciplinary teams to collaborate in real time.
- Quality Control: The system automatically conducts tests and validations to ensure that the product meets regulatory and quality standards.
- Cost Optimization: SAP PLM offers tools for cost analysis throughout the product lifecycle, enabling cost optimization.
- Integration with Other Modules: Once a product is developed, the system interacts with other modules, like MM (Materials Management) for materials management, and SAP ERP for logistics and finance.
- Product Tracking: Provides a complete history of each product, allowing companies a detailed view of all the stages it has gone through.
In summary, product lifecycle management in SAP PLM ensures that the entire process, from conceptualization to product retirement, is carried out efficiently and effectively.
2.2 Document and Specifications Management
Document and specifications management is another crucial component in SAP PLM, responsible for organizing and storing all relevant documents.
Key features:
- Secure Storage: SAP PLM enables secure and categorized storage of documents such as technical drawings, specifications, and manuals.
- Access and Retrieval: Facilitates quick access and retrieval of documents, which is crucial for maintaining a smooth workflow in the company.
- Collaboration: The system allows various departments to collaborate on documents in real time, ensuring everyone is on the same page.
- Integration with ERP: Once a document is stored or modified, the information is synchronized with other SAP modules, ensuring fluidity in business operations.
- Version Control: The system stores previous versions of documents, facilitating tracking of changes and past decisions.
Document and specifications management not only allows for more fluid and efficient operation but also plays a vital role in regulatory compliance and data-based decision-making.
2.3 Project and Portfolio Management
Project and portfolio management is another essential component within SAP PLM that provides the necessary tools for planning, executing, and monitoring projects related to product development.
Key features:
- Project Planning: SAP PLM allows detailed project planning, setting milestones, deadlines, and required resources.
- Resource Allocation: The system facilitates the allocation of human and material resources, ensuring that projects are carried out within the anticipated time and budget.
- Real-time Tracking: Offers complete visibility of the project’s status, allowing timely adjustments and data-based decision-making.
- Risk Assessment: Includes tools for identifying and managing risks, contributing to avoiding delays and cost overruns.
- Integration with Other Modules: This component also integrates seamlessly with other SAP modules, such as Finance and Quality Control, to offer a more holistic approach to product development.
In summary, project and portfolio management in SAP PLM is crucial for keeping projects on track, within scope and budget, ensuring success in the development of new products.
2.4 Integration with Computer-Aided Design and Manufacturing (CAD/CAM)
This component is responsible for the effective interaction between SAP PLM and computer-aided design and manufacturing (CAD/CAM) tools, crucial for more efficient product development.
Key features:
- Interoperability: Allows smooth communication between the PLM system and CAD/CAM applications, facilitating the transfer of designs and technical specifications.
- Version Management: SAP PLM manages different versions of designs generated by CAD/CAM systems, ensuring all teams work with the most updated version.
- Process Automation: Facilitates the automation of repetitive tasks in design and manufacturing, saving time and reducing the risk of human errors.
- Compatibility Checking: Before manufacturing, the system verifies the designs’ compatibility with manufacturing requirements, minimizing costly errors.
- Integration with Supply Chain: Once a design is finalized and approved, the information is automatically transferred to other systems like materials management and production planning.
This component ensures that computer-aided design and manufacturing capabilities are efficiently integrated into the product development process, speeding up production and improving the quality of the final product.
3.Submodules of SAP PLM
The SAP PLM module includes a variety of submodules designed for different areas of product lifecycle management:
3.1 Quality Management (QM)
- Responsible for ensuring and maintaining quality levels throughout the product’s lifecycle.
3.2 Document Management (DMS)
- Facilitates the creation, management, and archiving of all documents related to the product.
3.3 Project Management (PS)
- Allows the planning, execution, and tracking of projects related to product development.
3.4 Change Management (ECM)
- Assists in coordinating and executing changes in the product, from design to manufacturing.
3.5 Product Data Management (PDM)
- Stores and organizes product-related data, such as specifications and bill of materials.
4.Beneficios de SAP PLM
El módulo SAP PLM (Gestión del Ciclo de Vida del Producto) aporta diversas ventajas a las empresas, desde mejorar la eficiencia en la creación y mantenimiento de productos hasta facilitar la colaboración interna y externa. A continuación, se describen estos beneficios en más detalle:
4.1 Mayor eficiencia en el desarrollo de productos
Con SAP PLM, las empresas pueden acelerar el ciclo de desarrollo del producto desde la concepción hasta la producción y el mantenimiento. Esto se logra mediante una serie de herramientas que ayudan en la planificación, diseño, y pruebas, lo cual resulta en un tiempo de comercialización más rápido.
Características clave:
- Optimización de Recursos: La plataforma ayuda a asignar los recursos de manera más eficiente, evitando cuellos de botella y mejorando la productividad.
- Automatización de Procesos: Muchas tareas rutinarias se automatizan, lo que libera tiempo para centrarse en actividades más estratégicas.
- Toma de Decisiones Basada en Datos: La posibilidad de acceder a datos en tiempo real permite una toma de decisiones más rápida y fundamentada.
4.2 Mejora en la colaboración interna y externa
La colaboración eficiente es crucial para el desarrollo de productos, y SAP PLM lo hace más sencillo mediante herramientas que facilitan la comunicación y el trabajo en equipo tanto dentro de la organización como con terceros.
Características clave:
- Integración Interdepartamental: Al estar todos los datos y documentos centralizados, distintos departamentos pueden acceder a la información que necesitan para colaborar eficazmente.
- Comunicación con Proveedores: La plataforma permite una fácil comunicación y coordinación con proveedores y socios externos, lo cual es crucial para las etapas de diseño y fabricación.
- Transparencia y Trazabilidad: Todos los cambios y actualizaciones se registran, lo que facilita el seguimiento y la responsabilidad en los proyectos colaborativos.
4.3 Cumplimiento regulativo simplificado
Una de las ventajas más destacables de SAP PLM es su capacidad para simplificar el cumplimiento con regulaciones y estándares tanto locales como internacionales. Esto es especialmente crucial en industrias altamente reguladas como la farmacéutica, la alimentaria o la aeroespacial.
Características clave:
- Centralización de Documentación: Todo el papeleo y los documentos relacionados con el cumplimiento pueden ser almacenados y gestionados centralmente, facilitando el acceso y la verificación.
- Automatización de Procesos de Cumplimiento: SAP PLM puede configurarse para que automáticamente realice las comprobaciones de cumplimiento, reduciendo el riesgo de errores humanos.
- Actualización en Tiempo Real: La plataforma está diseñada para adaptarse a cambios en las normativas, garantizando que siempre estés al día en cuanto a cumplimiento.
4.4 Integración con otros módulos de SAP para una gestión coherente del producto
La compatibilidad de SAP PLM con otros módulos de SAP, como SAP ERP o SAP SCM, ofrece una visión unificada y coherente de los procesos de negocio. Esto no sólo facilita la toma de decisiones sino que también optimiza el ciclo de vida completo del producto.
Características clave:
- Flujo de Información Unificado: La integración con otros módulos asegura que todos los departamentos trabajen con los mismos datos, lo cual es crucial para una toma de decisiones precisa y eficaz.
- Optimización de la Cadena de Suministro: Al estar enlazado con módulos como SAP SCM, se puede tener un control más riguroso de la cadena de suministro, lo cual es vital para el ciclo de vida del producto.
- Consistencia de Datos: Al evitar la duplicación de datos y asegurar que todos los módulos estén actualizados, se garantiza la coherencia y precisión de la información.
Con estos beneficios, SAP PLM se erige como una solución integral que abarca desde el desarrollo y diseño del producto hasta su fabricación, distribución y mantenimiento, todo ello cumpliendo con los requisitos regulativos y de manera coherente y eficiente.
5.SAP PLM Implementation Process
5.1 Evaluation and Needs Analysis
The first crucial step in implementing SAP PLM is conducting a thorough evaluation of the company’s specific needs and requirements. This initial analysis is vital to ensure that the PLM solution is optimally tailored to the business processes and objectives.
Key features:
- Gap Analysis: Identification of gaps between current capabilities and future needs, helping to define the scope of implementation.
- Business Process Evaluation: Review of existing processes to determine which areas will benefit most from a PLM solution and where improvements are needed.
- Consultations with Stakeholders: Involving all stakeholders, from engineers and designers to sales personnel and management, to ensure their requirements are reflected in the system’s configuration.
- Definition of KPIs: Establishing key performance indicators that will be used to measure the success of the implementation and the ROI.
A well-executed evaluation and needs analysis lay the foundation for a successful implementation, ensuring that SAP PLM aligns with the strategic and operational objectives of the company.
5.2 System Configuration and Customization
Once the needs are identified, the next step is the configuration and customization of the SAP PLM system. This process ensures that the tool effectively adapts to the specific requirements of the organization.
Key features:
- Selection of Features: Choosing the components and submodules of SAP PLM that best fit the identified needs.
- Business Rules and Parameters: Setting up rules, workflows, and parameters that will guide the system’s operation.
- Data Integration: Importing and setting up databases and other systems to ensure a smooth and coherent transition.
- Configuration Testing: Validating the configuration through tests in controlled environments to ensure everything works as expected.
5.3 Training and User Education
Effective adoption of the SAP PLM system requires end-users to understand how to use it efficiently. Therefore, adequate training is essential for the success of the implementation.
Key features:
- Training Programs: Development and execution of training programs tailored to different roles within the organization.
- Documentation and Manuals: Providing user guides and training material as quick-reference resources.
- Practice Sessions: Offering users the opportunity to interact with the system in a controlled environment before live deployment.
- Ongoing Support: Establishing support channels to resolve queries and issues that may arise during system use.
Training and education are vital to ensure that staff can fully leverage the capabilities of SAP PLM, thus contributing to the achievement of the company’s business objectives.
5.4 Post-Implementation Monitoring and Adjustments
After the implementation and training period, it is crucial to establish a process for monitoring and adjustments to ensure that SAP PLM continues to align with the organization’s changing needs.
Key features:
- KPI Monitoring: Measuring and tracking key performance indicators to assess the system’s effectiveness in relation to the initial objectives.
- Functionality Audits: Regular reviews to ensure that all functionalities are being used as expected and that the system is adding value.
- Updates and Patches: Keeping the system up to date with the latest versions and security patches to ensure its integrity and efficiency.
- User Feedback: Collecting feedback and suggestions from users to identify areas for improvement and potential adjustments.
- Adjustments and Optimization: Based on the feedback and collected data, adjustments are made to the configuration, workflows, and other aspects of the system to improve its performance.
Post-implementation monitoring and adjustments are essential to ensure that the system remains relevant and effective, adapting to new business demands and challenges. This proactive approach facilitates continuous improvement and maximizes the return on investment in the SAP PLM platform.
6.Fictional Practical Example
6.1 Context and Challenges of Company I-57
Company I-57 is a fictional entity specializing in the electronics industry. Despite continuous growth, it faces specific challenges:
- Inefficient Product Lifecycle Management: Lack of a cohesive system to manage the development and production phases.
- Limited Collaboration: Communication and collaboration barriers among different departments.
- Regulatory Compliance: Difficulties in adhering to quality regulations and environmental standards.
6.2 Implementation of SAP PLM to Overcome Challenges
To address these issues, Company I-57 initiated the implementation of SAP PLM with the aid of a team of experts:
- Lifecycle Centralization: Integrated all stages of product development and production into the SAP PLM system.
- Improved Collaboration: With functionalities for sharing documents and data in real-time, they achieved greater cohesion among teams.
- Compliance Management: A specific module for handling regulations and standards allowed the company to stay up-to-date with less effort.
6.3 Results and Benefits Post-Implementation
After the implementation, notable changes were observed:
- Agility in Decision-Making: The availability of coherent data enabled managers to make informed decisions more quickly.
- Cost Reduction: The optimized system for product lifecycle management and regulatory compliance led to a significant decrease in operational costs.
- Customer Satisfaction: With a more agile and efficient product development process, the company could better adapt to market needs, increasing customer loyalty.
In summary, the implementation of SAP PLM transformed the operations of Company I-57, boosting both its efficiency and competitiveness in the market.
7.Integration of SAP PLM with Other Systems
7.1 Connection with SAP ERP
One of the most crucial aspects of SAP PLM is its ability to integrate seamlessly with other systems, particularly SAP ERP (Enterprise Resource Planning). This integration allows for a more cohesive and efficient workflow by centralizing relevant information and functions.
Key features:
- Bidirectional Data Flow: SAP PLM and SAP ERP share data in real-time, enabling a unified view of the product throughout its lifecycle and across different departments.
- Process Automation: The connection allows for the automation of various tasks, such as inventory updates, resource planning, and purchase order management.
- Regulatory Compliance: The integration ensures that both product development and business operations follow the same standards and regulations.
- Interoperability: Being part of the same SAP ecosystem, the transition between both systems is smooth, minimizing learning curves and accelerating adoption.
The integration of SAP PLM with SAP ERP not only brings benefits in terms of efficiency and smoothness but also improves product quality and customer satisfaction by ensuring a coherent and well-coordinated workflow.
7.2 Integration with Manufacturing and Supply Chain Modules
The interoperability of SAP PLM is not limited to SAP ERP. It also closely integrates with specialized modules that manage manufacturing and the supply chain, such as SAP MM (Materials Management) and SAP SCM (Supply Chain Management).
Key features:
- Information Unification: Being connected with these modules, SAP PLM allows easy and quick access to crucial data such as inventories, production orders, and bill of materials, all in real-time.
- Resource Optimization: The integration facilitates more precise and effective resource allocation, aligning product development needs with material availability and manufacturing capabilities.
- Traceability and Visibility: This connection provides complete visibility over the product lifecycle, from design to distribution, crucial for efficient supply chain management.
- Agility in Production: By integrating with manufacturing modules, SAP PLM facilitates a more agile workflow, allowing quick adjustments in production in response to changes in product design or market demand.
The integration of SAP PLM with specialized manufacturing and supply chain modules boosts efficiency across the organization. It allows for more accurate planning, reduces cycle times, and improves adaptability, ensuring that products are not only of high quality but also delivered timely and cost-effectively.
7.3 Synchronization with Other Product Lifecycle Management Systems
SAP PLM is not an island. Many companies already have other Product Lifecycle Management (PLM) systems in place when they decide to adopt SAP PLM. Therefore, it’s vital that it can effectively synchronize with other PLM systems in the business ecosystem.
Key features:
- Interoperability: SAP PLM is designed to work in harmony with other PLM systems, allowing for a smoother transition and parallel implementation if necessary.
- Efficient Data Transfer: Import/export tools and APIs (Application Programming Interfaces) facilitate secure and reliable data exchange between different PLM systems.
- Information Consistency: Thanks to synchronization, information like metadata, revision statuses, and change histories remain consistent across multiple platforms.
- Improved Collaboration: The ability to integrate with other PLM systems fosters interdepartmental collaboration and even between different companies, especially useful in large-scale projects involving multiple stakeholders.
Synchronization with other PLM systems enhances the versatility of SAP PLM, making product lifecycle management more coherent and efficient, regardless of the tools being used. This is crucial for companies seeking scalability and flexibility in their product development operations.
8.Conclusion
In today’s digital era, efficient management of the product lifecycle (PLM) has become a key pillar for any company looking to stay competitive. SAP PLM emerges as a robust and comprehensive solution addressing multiple facets of this business challenge. From the design and development phase to manufacturing and post-sales service, SAP PLM offers an integrated set of tools that drive operational efficiency, collaboration, and innovation.
Importance in Business Innovation: In a constantly evolving world, the ability to innovate rapidly is vital. SAP PLM enables companies to accelerate the time-to-market of new products, which in turn contributes to growth and competitive advantage.
Impact on Efficiency: By integrating different departments and functions within a single platform, SAP PLM minimizes information silos and optimizes processes, resulting in greater efficiency and cost savings.
Integration with Other Systems and SAP Modules: The cohesion between SAP PLM and other enterprise systems, both SAP and third-party, allows for a unified view and more effective management of the product lifecycle.
In summary, adopting SAP PLM not only optimizes product lifecycle management but also acts as a catalyst for innovation and business growth. In an increasingly saturated and competitive market, investing in an effective PLM solution like SAP PLM is undoubtedly a smart strategy for any company aspiring to lead in its sector.